Whether
you’re new to the industry or have been employed for a couple years, you can
always benefit from upgrading your metalworking craftsmanship.Where did you acquire your metalworking skills?
If polled, the majority of technicians would say they learned from their high
school or post-secondary collision repair educators. Still others may have
learned everything they know on the job. These are good sources for learning
metalworking skills, but if you’re looking to expand upon what you already
know, there are a number of sources that may be able to provide what you are
looking for.The following are examples:Rolling
Meadows, Ill.,-based I-CAR is a benchmark source for metalworking
information and training. The group’s curriculum includes Straightening
Steel Program 1 and Straightening Structural Steel Program 1, among other
related classes. Visit www.I-CAR.com and
click on “Training Courses” for more information. The
National Institute for Metalworking Skills Inc. (NIMS) is a non-profit
organization that was formed to support the development of a skilled
workforce for the metalworking industry, according to the group.
Some of their pursuits include developing, writing, validating and
maintaining skill standards for each industry; accrediting training programs
and assisting states, schools, and companies to form partnerships and
implement the skill standards. The organization can help you locate training
facilities in your area, as well as update you on industry standards.Another
useful tool that is right at your fingertips is the Internet. If you are
looking for more than just training, there are Web sites that can point you
in the right direction for tools and
even metalworking clubs. One such site, located at http://metalworking.com/links_to_learn.html,
includes a Frequently Asked Questions (FAQ) section and a variety of sources
including where to find books, tools and other training materials. But if you are looking for small class sizes and
a hands-on approach, Kent White, owner of TM Technologies, may be able to
fulfill your training needs. He has been working in the paint and metalworking
fields for more than 30 years. He teaches about 10 students at a time in his
workshop in Nevada City, Calif., and also travels across the country to conduct
seminars. His background is in automotive metalworking, as well as aviation and
airplane repair. “I call them metalworking intensives,” White says of his
seminars. “I teach them the principles of metal and how it moves.” The
four-day program costs $295 and includes meals, materials and supplies. Students
are sent a packet of workshop preparation materials, which contains five videos
and a study guide. They learn how to stretch, shrink, weld, form and shape
metal.As for the curriculum itself, White has developed
it over the course of teaching and asking questions of other metalworking
experts in the United States and Canada. “Training can be a lifesaver when it
comes to turning some guy loose on an expensive Volvo or Acura,” he says of a
shop owner’s peace of mind. “Bad habits can accrue way faster than you can
imagine. It’s just the little things that can make a big difference. For more
information, visit www.tinmantech.com
or call (530) 292-3506. If you’re looking for a more formal training
program or are interested in taking a few classes, your local community college
may have what you’re looking for.
There are also certain schools that have more specialized programs, such as
WyoTech in Laramie, Wyo., and Blairsville, Pa. The school offers training in
collision/refinishing, among other automotive training. Courses can run from
four to six weeks, and the entire program can be completed in nine to 12 months.
You can find out more information about the school’s offerings at www.wyomingtech.com.For those more specific questions that you
don’t necessarily need to take a class to find the answers, try contacting
your metalworking product supplier or jobber. They may have the answers you need
or be able to send you in the right direction as well.Becoming more educated in metalworking can give
you a leg up on the competition, as well as answer those nagging questions that
have been holding you back from your best repair performance. Just because
someone with more experience than you taught you a procedure doesn’t mean
it’s always correct. When in doubt, always double-check the procedures to make
sure you are working that pure metal shop magic.
About the Author
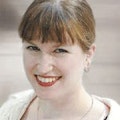
Lisa Greenberg
Prior to joining ABRN, Lisa served as an associate and later editor of a trade magazine covering the greenhouse industry. During her tenure there she wrote everything from news stories to feature articles that were designed to help greenhouse growers increase their business' profitability. She also traveled extensively in an effort to better understand the greenhouse industry. As editor, she spearheaded a redesign and refocusing of editorial content. Lisa began her journalism career by earning a journalism degree from Eastern Illinois University where she worked as a reporter for the Daily Eastern News.
Subscribe to our Newsletters