Integrating revolutionary technology into the spray booth
From the paint cup to the bottom line, 3M has a history of working with its customers to understand the challenges they’re facing and tracing them back to the basics and fundamentals of collision repair. Every challenge, no matter the size, presents an opportunity to help body shops improve their overall operations.
This philosophy of addressing every challenge guided the creation of the new 3M Performance Spray Gun. It’s designed to deliver superior performance on every front—material efficiency, increased comfort, reduced setup and cleaning time, energy use, and above all, results. The modular design that emerged from that process took nothing for granted.
Now, more than a year after its debut, the 3M Performance Spray Gun is the focus of a growing buzz about the benefits collision centers are seeing, both in the spray booth and on the bottom line. Going in, shop owners knew that the gun promised a simpler operation, lighter weight, and easier cleanup. What they’re discovering now is that its higher transfer efficiency at lower air pressures helps save on materials, save on downtime, and deliver quality work faster.
Jerald Stiele owns two Minnesota body shops, including Collision Center 1 in Golden Valley, Minnesota, where his two-painter team is finding measurable efficiency after switching to the 3M spray gun. They used to average as much as 2.6 ounces of paint per refinish labor hour, but after the change, they’ve come in under 1.5 ounces per hour for the same volume of work.
Stiele is one of several owners whose real-world experiences support 3M’s own research. In side-by-side tests with the same nozzle, material and pressure, the 3M spray gun delivered transfer efficiency improvements of between six and 18 percent compared to competitors’ guns. As 3M Product Developer Ryan Erickson explains, “the value driving this entire product is to save the painter time. The efficient use of air is what leads to the efficient use of paint.”
The nozzle makes the biggest difference from product to product — for example, from primer to metallic base coat. At the microscopic level, spraying paint is really shearing droplets apart by force, and the results had to be consistent. In particular, Erickson said, the designers aimed to keep transitions smooth at the edges of the spray pattern. When the distribution of paint changes gradually instead of abruptly, it’s easier for painters to produce consistent results.
3M’s design team used virtual product development tools, computational fluid dynamics, and finite element analysis to design the spray gun. Even before building the first prototype, they were able to run fluid simulations in the computer that modeled the air flow and material transfer at given air pressures.
Using less pressure is always a plus. In paint spraying, air pressure is energy. Because the spray gun delivers higher transfer with less air pressure, shops can do more than just save on energy—they can put more paint on the panel and lose less of it to the surrounding air.
In their early experiences with the new spray gun, painters mixed the same amounts for each job they were accustomed to. When they started finding more unused paint in the cup, job after job, they realized they could mix less to begin with. “There was a learning curve, but our painters trust that they can mix less now,” Stiele says. “They’re going between jobs a lot quicker, and their productivity levels are a lot better.”
Ernie Loggarakis is the owner of Nick & Ernie’s Fix Auto in Skokie, Illinois, which handles about 170 cars a month. Loggarakis equipped his whole team with the new 3M spray gun in summer 2021, and says, “the technicians gave me positive feedback right away: The biggest thing we’ve seen is a 13 percent savings in material, and that money goes right to our bottom line. It makes us more profitable in a tight market.”
Loggarakis says using less paint is only part of the spray gun’s appeal. “The spray gun seems to atomize the product more evenly, and gives a nicer pattern,” he says. “More of the material from the spray gun gets onto the car.”
By changing nozzles and settings, the spray gun can handle solid colors, metallics, pearls, clear coats, sealers, and primers, all at the same high transfer efficiency and consistent atomization. The spray gun works with either gravity-feed or pressurized supply systems. Because paint never enters the body of the gun itself, end-of-day cleaning uses less time and less solvent. And because it’s the lightest spray gun on the market, it increases comfort.
At Concours Auto Works in Milwaukee, owner Emil Belich reports a similar experience. Belich’s team uses the new spray gun for clear coat and are now getting the same results at 10 psi that they used to get at 30.
“I’m a believer in low air pressure,” he says. “If you don’t blow paint on the car, it goes everywhere else. The 3M spray gun’s atomization at lower air pressure was a new experience for me.”
As Belich notes, superior atomization means more than waste reduction: Consistent volume at pressure is also critical to color matching, and less overspray means less mess. At too high a pressure, he says, “it sticks to the lights, it sticks to the filters, it sticks to your body. With the 3M spray gun, the cleanliness of my paint jobs is off the chart.”
To Stiele and the other owners, the needle in the spray gun isn’t the only one they’re keeping an eye on. There’s the one that tracks their financial performance against tight margins—and saving time and material cost in the paint booth helps it point in the right direction. “A little movement of that needle has a great effect on the bottom line,” he says.
About the Author
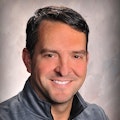
Corey Munn
Over the last more than years, Corey Munn has served as global paint applications segment leader for 3M Automotive Aftermarket Division. In this capacity, he leads global commercialization of 3M's business into paint application processes, encompassing both automotive aftermarket as well as industrial coatings. Prior to this role, he served in business leadership roles with 3M that span both industry (electrical and performance material additives) and geography (Europe and Middle East and Africa).