Maximizing productivity and reducing material waste in the prep and paint areas
A modern-day body shop’s functionality is a complex ecosystem. From a high-level perspective we see two functioning pieces: you have the front office, and you have a shop floor. Within these two sections of the shop, you can break it down further. The front office is mainly comprised of estimators, managers, and receptionists. The shop portion is made up of five major sections: parts, body repair, paint prep, paint, and detail / paint correction. Each one of these pieces of the body shop puzzle interlocks with one another to smoothly, effectively, and efficiently repair a vehicle after the event of an accident. Often when looking to improve the shop’s efficiency, we gravitate toward the paint shop, as it is generally considered a bottleneck by many. This can be caused by many small or large inefficiencies that all add up, creating this bottleneck area where challenges can sometimes arise.
One may think that improving the painter’s efficiency could be as easy as installing another prep deck, adding another booth, or adjusting the products used. Many times, shops have other factors that can cause inefficiencies for their painters. Looking at the repair processes involved prior to painting, we see a variety of potential challenges. These additional challenges that we most frequently witness are related processes prior to the painter getting the vehicle. Now, before I go on about these challenges, I want to preface that the body tech and paint tech’s expectations from each other need to be of equal value to ensure vehicle flow-through is as smooth as possible.
Body filler pinholes
An example of this type of challenge includes pinholes. Pinholes are small holes in body filler that are considered a defect. Sometimes pinholes are caught post-filler application, in which case, they can be fixed prior to moving to the paint shop. However, when pinholes aren’t seen during the filler application and sanding process, the last resort for some paint techs is to try to prime them out — or, best case — they are required to send the vehicle back. Regardless, both cases slow down the painter’s efficiency, due to the prepper/body tech having to spend additional time trying to prime pinholes out or having to fill the place of that vehicle if sent back. Even if someone primes over a pin hole, there is no guarantee that pinhole won’t cause a future failure resulting in rework. If not seen before the paint process, the paint job will likely have a defect that is no longer able to be fixed without rework.
Priming
Furthering into the repair processes, it's no secret that the priming process can greatly affect a painter’s productivity. If done correctly, it can certainly improve overall productivity and if done incorrectly may greatly hinder a painter’s output. While many of us do not think much about this simple yet complex procedure used in many repairs, it can be a challenge for a painter with space limitations and timelines to properly prime a repair area on a vehicle. Proper priming can eliminate the need for a reprime, or in worst cases, a complete redo of the job. It’s imperative that a technician not only mixes primer to the paint manufacturer’s recommendations, but also properly sets up his or her spray gun and adequately maintains the equipment. Let’s face it; often the primer gun at a shop is a hand-me-down, beat-up spray gun that no longer served the purpose of topcoat-spraying or is a very cheap inefficient spray gun that many would say is “good enough."
Many times, I see people using these “good enough” spray guns spraying at ultra-low pressure to help keep overspray down. While they are trying to minimize overspray, they are disregarding what is truly the issue in their equipment. Furthermore, what is likely happening to the primer as they spray? Spraying at ultra-low non-recommended pressures causes the material to glob up and not properly atomize. In turn, the primer is loaded with solvents, giving it a higher chance to run or sag. Not only that, but the bigger issue is that the primer has a greater likelihood of solvent popping and/or shrinking causing a visible repaired area. Choosing equipment that has a high transfer efficiency allows the tech to achieve proper atomization levels and can alleviate the issues of primer problems resulting in faster throughput in the paint shop.
Proper preparation
In the pursuit of reducing waste within the paint area of a body shop, particular attention must be paid to the meticulous preparation of surfaces prior to painting, especially when it comes to pinholes and priming. Imperfections such as pinholes in the body filler can become a significant source of waste if it’s not properly managed. To mitigate this, technicians should correctly mix and apply body filler to prevent air entrapment and ensure an even pinhole-free surface. This not only streamlines the process but also reduces the need for rework as well as excessive priming. By its nature, this can be wasteful due to having to prime over the same repair area multiple times. The use of a properly maintained high transfer-efficient spray gun in conjunction with following the manufacturer’s recommendations on mix ratios, spray gun tip sizes, and spray gun setup can prevent overapplication. This, in turn, reduces how much primer is needed to complete a job. By focusing on these two areas, pinhole prevention and priming, body shops can cut down on material waste generated by unnecessary steps and achieve overall productivity gains in the paint shop.
In summary, the efficiency of a body shop hinges on the seamless integration of its front office and shop floor operations, with the paint shop playing a pivotal role in the overall workflow. Through addressing the root causes of inefficiencies, particularly in the overlooked areas of pinholes and priming, improvements can be made to a painter’s productivity. In addition, this can lead to a reduction in their overall waste generated. By implementing best practices in filler application and mixing as well as following paint manufacture recommendations, body shops can overcome these challenges. This will lead to a more productive painter and less wasted material generated in the process, ultimately contributing to a more profitable, productive body shop.
About the Author
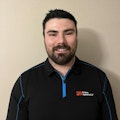
Connor Alexy
Connor Alexy is an application engineer at 3M in the Automotive Aftermarket Division, focusing on the paint shop side of collision repair as well as adjacent markets. He has worked in and around the industry for eight years in a variety of roles, from working in shops to technical testing and training. Connor holds a bachelor’s degree in Applied Technical Management / Leadership as well as an AAS in collision repair from Dunwoody College of Technology.